For all industrial stakeholders, training new entrants is a significant investment of energy, time, and money. Bridgestone, a leader in tire manufacturing, has invested in blended learning combining face-to-face training, Virtual Reality (VR), and simulation in a training mini-factory produced by Audace.
Device
Audace has recreated a complete production line and various machine tools for Bridgestone. Seven workstations and associated operations are simulated.
The operator navigates in their virtual environment using a VR walking pad. They can perform virtually all tasks required for tire assembly and acquire precise technical skills as well as learn how to monitor checkpoints.
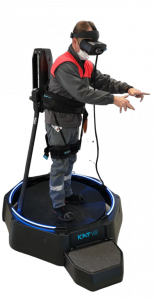
Multiple levels of difficulty and scenarios are incorporated to provide progressive and safe training without the requirement of an operational real machine.
The trainer receives visual feedback on the screen. He can track the results and intervene to reinforce a point or overcome a difficulty.
Since its introduction in France, this VR simulator has been awarded the “Bridgestone Group Award for Management Fundamentals” and has been developed for Spain (B-Kanpus, Bilbao). It is currently being deployed in Hungary and Poland. The concept has been expanded to new production processes such as Quality Control and Mixing (Banbury).
Objective
By overcoming the challenges of hiring and training at Bridgestone, the VR simulator allows unemployed individuals with no prior manufacturing experience to acquire the necessary technical skills and the right pace to work on a tire assembly line without experiencing the stress associated with real production.
Keys to the success of the simulator
1. Hyper-realism
The high-quality 3D graphics of the simulator create a complex environment that immerses the learner, making it indistinguishable from real-life situations.
2. Presence
The learners immediately feel connected or present in this environment. Indeed, this immersive learning has the tremendous advantage of being multi-sensory. It requires:
- motor functions (involvement of the body in action through the VR treadmill, resistance to effort, ability to repeat precise movements, etc.),
- sensory functions (sound, vibration, etc.; for an optimal immersion, the sounds of the workshop and the production line have been reproduced),
- emotional functions (building self-confidence, testing one’s limits, developing vigilance).
3. Realisation
The mechanism by which success is measured in the immersive learning environment is related to real performance objectives. The device itself is adapted to the target audience, namely the Generation Y. Learning involves engaging activities similar to video games that are commonly practiced in private settings, which can generate immediate enthusiasm among learners.
ROI of the simulator
Thanks to the digitization of its training program, Bridgestone Bilbao has observed the following return on investment (ROI):
• 80% reduction in the immobilization of production resources required for training
• 90% reduction in the immobilization of human resources required for training
• 30% to 50% reduction in safety incidents
• 30% to 50% reduction in quality issues
Outcome: 70% cost savings on the total training expenses.
Besides the other impacts :
• National company image (frequent articles in national media + Visit of the Prime Minister of the Basque Country)
• Enhanced local corporate image
• Company image within the industry (clients/suppliers)